
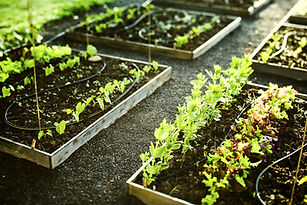
Financial Projections
The financial projections of our product can be estimated based on net income, liquidity, and solvency. Net income refers to the surplus of revenues that the company makes over initial expenses. Liquidity refers to the money that is used to pay off bills. Lastly, solvency refers to the relationship between the company’s assets and liabilities.
​
Our company would first need a startup investment that would cover the production of our units and the shipping of our products. It is projected that these costs would be roughly $30,000 for a prototype unit. In the first five years of our company, we require a small office space technology to access and develop our website and social media. As our company continues to sell composting units, we will be able to obtain more revenue and expand our services. By expanding to the West Coast in cities like Los Angeles and Seattle, we will increase our market and continue to maintain revenue. Throughout this process, we would continue to create partnerships and spread awareness about our product.
First, we would need to consider the cost of the shredder piece of our unit. We have recently been in contact with JWC, a shedder manufacturing company. They have told us that their smallest current model, the (1-SHRED-H-0800), could be sold to us at roughly $13,000. Even with their smallest model, our design could still perform optimally and could possible use an even smaller model for increased efficiency. In response, JWC said that they may have an even smaller model in the future. Using this information, it is estimated that our design's shredding component will cost roughly $10-13,000 given current projections for technological development.
​
The next part of our unit is the solar panels that would power the shredder and drum. To perform these functions, a 265-watt solar panel with 60 cells or more would be required. Using this information, we have found that this would cost roughly $2,000. Solar panels at this price can be found from companies such as Larson Electronics LLC. This company also sells frames for solar panels at about $500.
​
Dumpster shells are also critical components to obtain to produce our product. Because we are reusing dumpsters, we can obtain them for extremely low prices through partnerships with local city governments. It is estimated that we could purchase a used dumpster at roughly $1,000. There is also the option of salvaging in dumps to try to obtain the dumpster shells for free, saving the company even more money.
The welding process of our dumpster shell is another expense that needs to be taken into consideration. Because the amount of money spent on welding will be case-by-case depending on how damaged the dumpster is, the welding could cost anywhere between $1,500 and $6,000. By developing partnerships with welding shops and providing regular business for them, we could decrease these prices.
​
Lastly, the cost of the battery must be considered. In the current market, batteries that would be used in our units cost approximately $4,000 to $5,000. Because it is powering a rotating drum, the battery needs to have the capabilities to store the large quantity of energy that is produced from the solar panels.
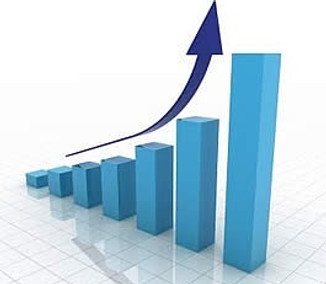
